Unlocking the Power of Metal Stamping: Techniques for Boosted Item Advancement
In the realm of production, the usage of steel stamping holds a significant area due to its adaptability and performance in creating detailed parts and elements. However, real potential of steel marking stays untapped by lots of firms seeking to enhance their product growth processes. By exploring advanced approaches and techniques tailored to enhance design, material choice, manufacturing efficiency, and quality control, companies can open a wealth of opportunities to raise their products to new heights of technology and efficiency.
Advantages of Metal Stamping
Metal marking offers a effective and economical approach for creating high-quality steel parts. One of the crucial advantages of steel stamping is its ability to create complex geometries with high precision and consistency.
Additionally, metal stamping permits for high-volume production, making it excellent for projects that require big amounts of steel elements. The speed and repeatability of the stamping procedure not only make sure expense financial savings however likewise contribute to faster turnaround times for production orders. Additionally, the usage of automatic equipment in steel marking aids lessen the risk of human mistake, bring about boosted total product quality.
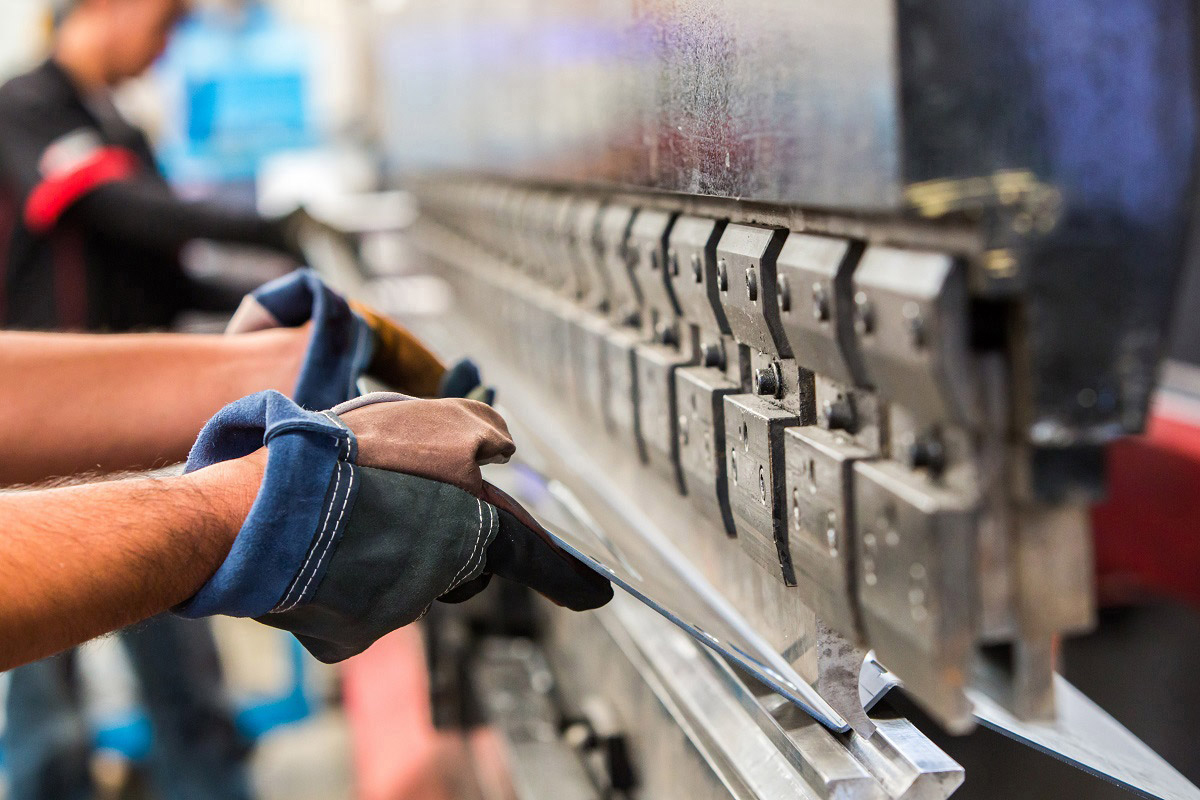
Design Optimization Strategies
Through cautious consideration of material residential properties and geometric configurations, style optimization methods play a vital function in enhancing the effectiveness and functionality of steel stamping processes. By purposefully analyzing elements such as material thickness, stamina, and kind, manufacturers can tailor the style to make the most of the efficiency of the marking procedure. Making use of simulation software program, designers can predict how different design variants will behave under different stamping conditions, enabling the recognition of potential concerns prior to manufacturing starts.
Additionally, integrating attributes like fillets, chamfers, and embosses into the style can boost the total high quality of the stamped component while minimizing the danger of issues such as cracking or buckling. Furthermore, maximizing the layout of attributes on the component can enhance the material flow during stamping, causing more consistent and specific results.
Essentially, layout optimization techniques enable manufacturers to adjust their metal marking procedures, leading to boosted product top quality, boosted production efficiency, and inevitably, a much more competitive setting out there.
Product Selection Approaches
Style optimization techniques in metal marking processes greatly depend on strategic material option approaches to make sure the desired performance and performance of the produced components. The selection of material in metal marking is crucial as it directly influences the quality, sturdiness, and general capability of the final item. When selecting the appropriate product for a particular task, factors such as mechanical properties, cost-effectiveness, formability, and deterioration resistance should be considered.
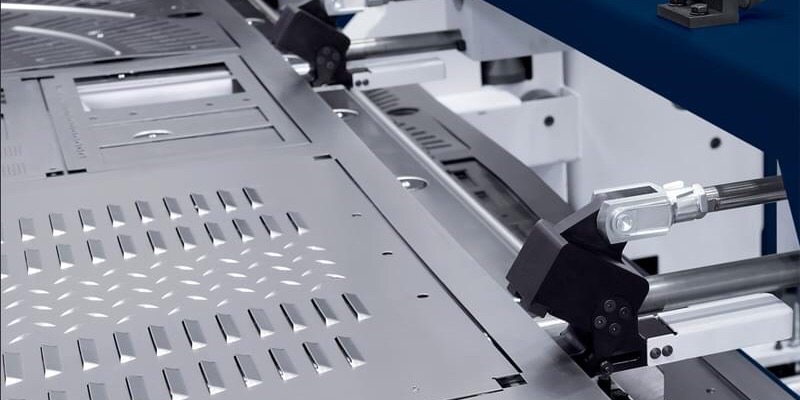
Additionally, cost-effectiveness plays a considerable function in material choice techniques. Stabilizing the efficiency needs with the general cost of products is necessary to ensure the economic practicality of the production procedure. Furthermore, considering aspects like recyclability and ecological impact can additionally this link enhance the sustainability of the picked material. By carefully reviewing these elements, suppliers can enhance their material choice techniques to accomplish remarkable item high quality and operational performance.
Enhancing Production Performance
Effectiveness in manufacturing procedures is a crucial element for making sure cost-effectiveness and prompt distribution of high-quality steel stamped parts. To boost manufacturing efficiency in metal marking, a number of methods can be executed.
Additionally, executing automation and robotics in metal marking procedures can significantly increase performance and uniformity while reducing labor prices. Automated systems can do repetitive jobs with high accuracy and speed, resulting in enhanced manufacturing effectiveness and greater outcome prices. Buying modern marking equipment with innovative attributes, such as servo-driven presses and fast die change systems, can better optimize production procedures and lessen downtime.
Furthermore, developing clear communication networks and fostering partnership between design, design, and production teams is essential for identifying prospective bottlenecks and executing continual improvements in the manufacturing workflow - Metal Stamping. By welcoming lean manufacturing concepts and leveraging technology improvements, manufacturers can unlock the complete possibility of steel stamping processes and accomplish better production effectiveness
Quality Assurance and Examination Methods
To make sure the constant manufacturing of high-grade steel marked components, rigorous quality control and evaluation methods play an essential duty in confirming the accuracy and honesty of the production process. Quality control in metal stamping involves a series of systematic checks and steps to ensure that each part meets the given demands. Examination approaches such as aesthetic assessment, dimensional analysis, and material testing are commonly utilized to assess the high quality of stamped parts. Aesthetic inspections ensure the surface area coating and stability of the components, while dimensional analysis verifies that the components adapt the needed specifications. Product screening right here methods like hardness screening and material composition analysis assistance verify the product residential properties and structural stability of the stamped parts. In addition, advanced technologies such as automated optical examination systems and coordinate measuring machines are progressively being utilized to enhance the precision and performance of quality assurance procedures in steel stamping. By applying robust quality control and examination techniques, manufacturers can maintain high standards of quality and uniformity in their metal stamped products.
Verdict
To conclude, metal stamping deals countless advantages such as cost-effectiveness, precision, and versatility in product advancement. By applying design optimization techniques, choosing ideal products, and enhancing production efficiency, producers can attain better products with decreased lead times. Quality control and examination methods play a vital duty in ensuring the end products fulfill the required standards. In general, unlocking the power of metal marking calls for a calculated method to enhance product advancement procedures.
Steel stamping offers a affordable and effective method for generating high-quality steel components.Additionally, metal marking enables for high-volume production, making it ideal for tasks that need large amounts of metal components.Through mindful factor to consider of material buildings and geometric setups, design optimization strategies play a critical function in enhancing the performance and performance of metal marking processes.Layout optimization strategies in metal marking procedures his response heavily depend on tactical product choice strategies to make certain the preferred performance and effectiveness of the manufactured components. The choice of product in metal stamping is essential as it straight affects the quality, resilience, and total functionality of the last product.